SER Blog Customer Stories & Use Cases
Document management reloaded at Duravit
Julia Pedak
Duravit is known for helping its customers to design and create the bathrooms of their dreams. And innovation plays a key role here. From bathtubs with an integrated sound module, to sensor-controlled bathroom lighting, to smart whirlpool and wellness systems: the manufacturer of designer bathrooms offers its customers innovative technologies and operates in more than 130 countries worldwide. How does the company set itself up for successful global cooperation between all of its locations? With an enterprise content management (ECM) platform. It supplies the right information to employees around the world and is the basis for customer-centric processes.
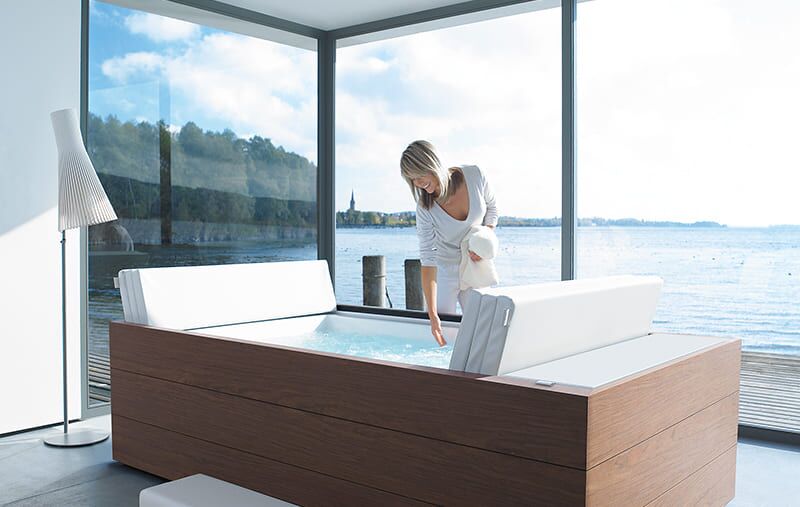
From classic and functional to upscale and exclusive, Duravit has been inspiring customers to create their dream bathroom environments for over 200 years now. Founded in 1817 in southwestern Germany as an earthenware factory, the Duravit group now comprises 12 production sites in Germany, France, Egypt, China, India, Tunisia, and Turkey. More locations and customer projects also mean an increasing amount of information: the volume of documents is growing by one to two million documents a year. In 2010, the archive was more than 10 years old and was no longer up to the task. It lacked key functionalities, such as detailed cross-tenant authorizations, which posed a compliance risk, especially when dealing with customer data. The old archive was also no longer suitable for international business processes. With 6,400 employees from 50 or so different nations working together worldwide, this was a real problem. A modern, sustainable alternative had to be found: an innovative ECM platform that could be used throughout the company.

One platform – unlimited solutions
Duravit uses Doxis throughout the company and around the world. Find out here how you can use the ECM platform for a wide range of use case scenarios.
Read nowArchive reloaded
Before Duravit could launch the new ECM platform, it was time to say goodbye to the old archive. Around 20 million documents had to be migrated. Werner Hoeltl, Application Manager (Finance) at Duravit AG, explains: “We realized beforehand that it was impossible to transfer several million documents at the snap of a finger.” With the right migration concept, the impossible became possible, without even interrupting operations. Working together with the SER Group, all documents were migrated and are now stored in an audit-proof manner.
A 360° view of customers & suppliers
When it came to choosing the right ECM platform, Hoetl says, “It was important for us that we choose a vendor with strong in-house software development capabilities that would fulfill European legal requirements.” Duravit decided that the ECM platform Doxis could fulfill these requirements while also bringing together all information related to customers and suppliers.
The first step was to launch customer eFiles. Up until then, communication between the different locations took place by phone, email, or on paper, which was a manual and time-consuming process and entailed a great deal of searching, particularly in the case of requests across the sales area. With the customer eFile, this problem was solved: national and international departments find the information they need regardless of location – also from the integrated ERP system Infor and the international company network. This means that they always have all customer information to hand and can provide information whenever it is needed.
Duravit also uses the ECM solution for communication and collaboration with suppliers across the globe. Supplier eFiles document the entire life cycle of business relationships: The purchasing teams at Duravit’s international locations find current orders, order changes, on-call orders, delivery notes, and Infor data. The next process improvement is already in the pipeline: automated inbound mail processing. ECM platform will soon facilitate the assignment of inbound emails and other documents from various channels automatically to the appropriate customer or supplier eFiles. As a result, employees around the world will immediately find correspondence with customers and suppliers in the right business context.
Up to date anywhere and anytime: eFiles for QM & PM
Since the introduction of the first eFiles, communication between the international locations and Duravit headquarters has streamlined considerably. It’s no wonder then that Duravit wants to expand the ECM platform further: eFile solutions and workflows for the areas of product management (PM) and quality management (QM) are already being implemented. It is precisely these departments that must ensure that all international Duravit locations can work with the same assembly and installation instructions, for example. "It shouldn't matter if a sink is produced in Germany, France, or Egypt – every location must have unlimited access to the assembly details, e.g. the space between two holes including the allowed tolerance value," explains Hoeltl. Instead of storing the documents on Windows Explorer drives and organizing communication via time-consuming email correspondence, QM and PM teams process them directly in the ECM system. For example, if a product description changes, the new version is available immediately for all locations. Today, there is no need to worry about production errors caused by outdated information.
Audit-proof archiving of invoices & emails
One advantage of the ECM platform is that it makes information from the different applications available and archives it securely. In 2013, Duravit therefore linked its workflow to electronic inbound invoice processing. The ECM solution digitizes all inbound paper invoices, assigns a barcode to them, and archives them in an audit-proof manner. Duravit’s accounting department can then process the invoices further using Infor. This saves time and prevents errors that can occur if work is carried out manually. The system also documents the entire invoice process in a traceable manner. This also applies to sales tax-related emails. They are stored automatically pursuant to applicable law. During a tax audit, all required documents are available at the push of a button.
EDI archiving: Keep track of customer wishes
Gold-plated handles or faucets? Duravit takes pride in fulfilling its customers’ precise wishes. Employees make a note of these simply as remarks in EDI orders. If customers have any questions later on, however, the responsible service employee currently has to ask the IT department whether the special request was documented in the original EDI. To streamline and speed up this process, Duravit is planning to launch audit-proof archiving of EDI data with ECM.
The article was first published in German in the December 2019/January 2020 issue of the German publication Wissensmanagement Magazin.
The latest digitization trends, laws and guidelines, and helpful tips straight to your inbox: Subscribe to our newsletter.
How can we help you?
+49 (0) 30 498582-0Your message has reached us!
We appreciate your interest and will get back to you shortly.