SER Blog Customer Stories & Use Cases
ECM and BPM at Neways Electronics Riesa
Bärbel Heuser-Roth
Neways Electronics Riesa (formerly known as BuS Elektronik) produces customized circuit boards and electronic assemblies. The electronic manufacturing service provider adjusts its production to customer requests for changes. With Doxis, the production team immediately receives all documents related to the changes. Digital production records and workflow-supported change and documentation processes now effectively support Neways Riesa in process engineering, quality assurance and production.
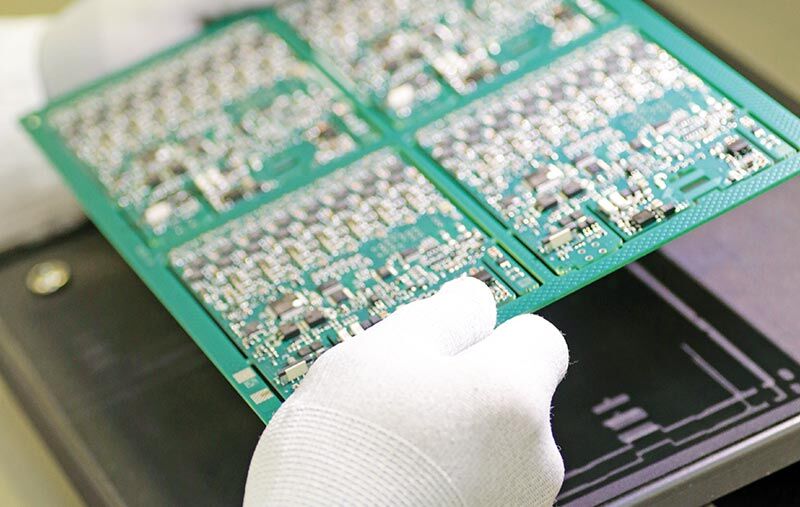
In the past, complex plans for the positioning of assembly parts on circuit boards were always copied and printed out. Over time, employees had a hard time reading the finely printed component references and polarities. "We would divide up intricate drawings into sections to take a closer look at the details. At a certain point, though, it's just not possible to do this anymore on paper," explains Falk Müller, Process Engineering Manager. What's more, schedules, assembly instructions and circuit diagrams took up a lot of space. These documents were manually sorted into records and distributed to production — which cost valuable time. To ensure that customer wishes were immediately implemented, all of the relevant production documents needed to be up-to-date and directly on hand. This is now possible thanks to electronic records and digital workflows.
Proven concept — fast implementation
The ECM system Doxis, with its modern interface, user-friendliness and comprehensive parameter options, convinced Neways Riesa to go with SER. The multilingual capability of the software and the option of launching eRecords in other parts of the company were also important in its decision-making process for a new system. In early 2015, the ECM project kicked off with an extensive needs analysis conducted by SER's ECM experts. The test phase took place in the spring, followed by the set-up of a production system, employee training, and the installation of the software in the Process Engineering and Quality Assurance departments. Already a half-year later, Neways Riesa was able to go live with the system.
Information and processes united
Digital documents and electronic production records support production and quality assurance at Neways Riesa. To accomplish this, Doxis combines ECM and BPM on one technology platform and thereby connects information and processes. Schedules, parts lists, circuit diagrams and the related work instructions are stored in the electronic production records. There, the production team has direct access from their workstations, which are gradually being equipped with computers. Doxis manages the processes for creating and changing documents in the Process Engineering department and for verifying and releasing documents in the Quality Assurance department (through the Process Engineering Manager). This means that new and updated documents can be directly passed on to production without losing time.
From a legacy archive to a new standard
About 3,000 product types currently require production records at Neways Riesa. Since Doxis was launched, more than 3,500 files and over 320 eRecords were created from the paper-based archive; another 800 new eRecords are added each year. To create new documents, the company uses templates which are filed in Doxis. This means that production documents are standardized for production processes and information. They have, for example, consistent document headers with the corresponding component names. In preconfigured fields, the employees see which further information is needed. This helps not only to create complete documents, but also to quickly view them. Doxis can also link production records to customer documents, e.g. to orders or emails with customer change requests. All documents relevant to production are therefore brought together in the context of the production order and can be found easily using the versatile search function in Doxis. Compared to the previously slow searches through paper plans and documents, the improvement was immediately perceptible: "When you think about the fact that some circuit boards contain several thousands of components, you realize how much easier work is now," explains Christian Döring, Process Engineering employee.
Quick changes, perfect quality
One important tool at Neways Riesa is the change notification database, which was developed in-house to issue and manage notifications of changes. The notifications are issued as forms with detailed information about the changes, covering the validity date, the affected assembly group, the scope of the change, the name of the related work order, etc. By integrating the change notification database into Doxis, change notifications are displayed every hour in the digital cover sheet of the production record. This enables Neways Riesa to incorporate customer changes into the ongoing production process. Of course, the quality must remain consistently high, even when the changes come at short notice. For this reason, Doxis offers an interface to the ERP system of Neways Riesa. Work schedules saved in the ERP system can be directly compared, for example, with the documents of the electronic production records to check that processes are being correctly implemented and that Neways Riesa's high quality is ensured.
On the agenda: company-wide ECM
Neways Riesa wants to launch Doxis in areas beyond the Process Engineering and Production departments. This was something that the company considered already when selecting the software solution, as Falk Decker, Data Processing Manager, explains: "It was our goal from the beginning to launch an ECM solution that not only fulfills the requirements of the production record, but also can be expanded to other corporate areas as well as document and record types." Besides digitally managing contracts, delivery notes and invoices, the company would also like to have electronic customer records that are accessible across all departments. This would streamline the offer creation and order process and provide Neways Riesa customers even better service.
Bärbel Heuser-Roth
For many years now, Bärbel Heuser-Roth has been dealing with a wide variety of ECM topics, from information logistics, process management and compliance to the use cases of intelligent processes for automated information management. She has also spent her career researching and writing about the implementation of ECM projects at companies and organizations.
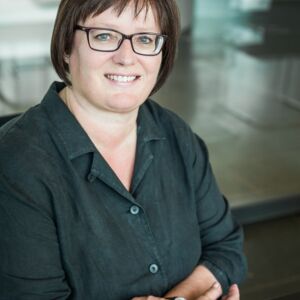
The latest digitization trends, laws and guidelines, and helpful tips straight to your inbox: Subscribe to our newsletter.
How can we help you?
+49 (0) 30 498582-0Your message has reached us!
We appreciate your interest and will get back to you shortly.